Test benches: production test and test systems
In an initial phase of product specification or its associated costing, we often think about design (mechanical, electronic), software development, design and realization of various tools, prototypes, pre-productions.
Certification is sometimes mentioned but the development phase of the production test system is very often forgotten because it is difficult to predict the impacts, costs in resources and test equipments. In addition, the development schedule is often very tight and customers ask to absolutely follow the «Go To Market» of the product. This suggests that manufacturing testing (mainly electronic testing) is often left out of the process because it is perceived as a time-consuming step that slows development.
However, this step is key to ensure that your products will come out of production in accordance with your specifications and with the required level of quality. A non-compliant product from your manufacturing lines is expensive to repair or replace and damages your reputation near distributors or end customers.
Design for Test
The testing strategy should be considered as early as possible in the product design to ensure that the product will be testable and that it will be possible to implement the electronic testing sequence to be performed in production to ensure that the product is reliable without failures or drift over the production batches.
In the design phase, it is important to define from the schematic the essential elements that need to be checked, either during qualification or in mass production. It is then necessary to implement test points on the printed circuit board (PCB) accessible for the various means to be implemented (test probes of measurement instruments, connectors, probes on bed of nails). They will be useful for connecting the test benches to the electronic board.
The conditions of use of the products (temperature, type and quality of feed, for example) must also be taken into account to define the equipotentials to be monitored and measured in order to ensure the proper functioning of the product in all its use ranges.
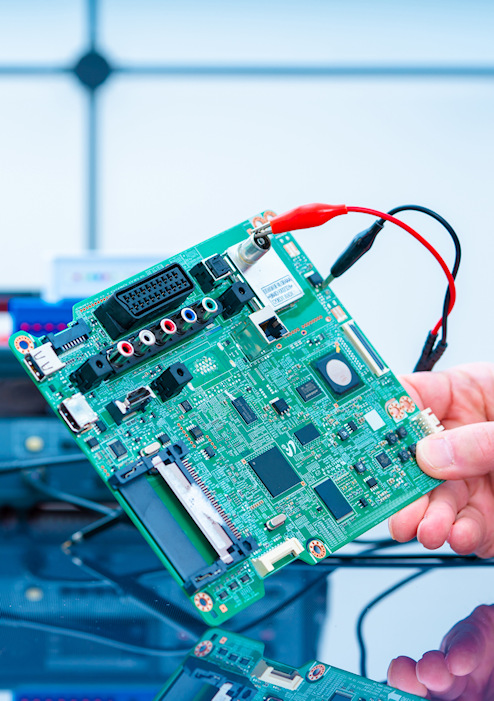
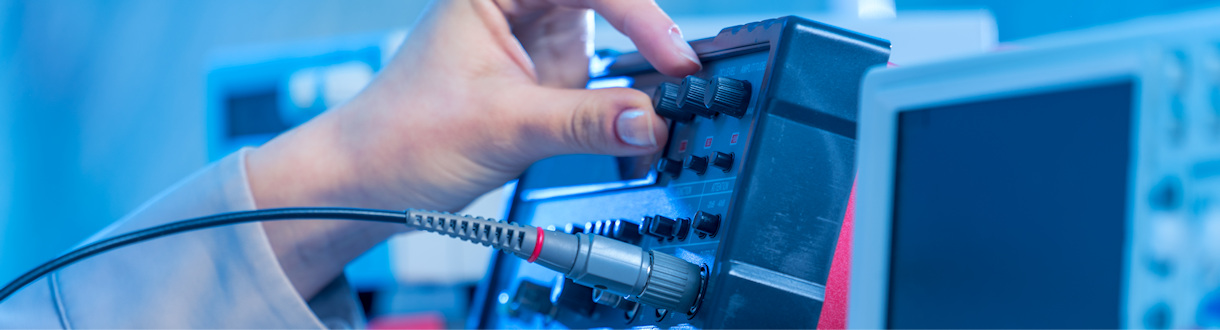
Qualification
Product qualification occurs at several stages of design and industrialization.
First of all, during the design phase, it’s important to ensure that the product architecture functions correctly by checking the compatibility of output and input signals between the various functional blocks of the product. The energy consumption of the product must also be calculated theoretically, if it is energy autonomous.
During the EVT/DVT prototype phases, these data are correlated with measurements made on manufactured products in all temperature and power ranges. It is necessary to check that the response of the components complies with their specifications and that the complete electronic function meets the expressed need and the desired operation.
This is where the functional test specification in production begins, for the development of electronic test benches.
In the pre-production phases, a further qualification on a larger number of pieces is carried out in order to confirm the measurements and calculate the dispersion of the electronic functions. These measurements will complete the functional test specification by integrating the acceptance margins of automatic tests made in production.
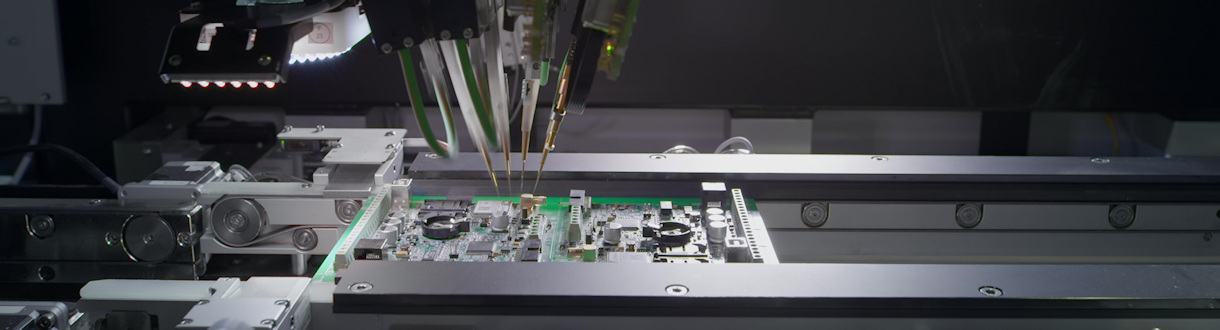
Production test
Production test allows to differentiate the products deemed correct from the products presenting a defect and refused.
Different types of tests can be performed on a product before the production. These tests include in-situ, functional test, and safety level tests.
In-situ tests: an in-situ test involves testing the components of an electronic board and can confirm that no components are missing, that no short circuits are detected, and that all components are properly soldered. An additional optical inspection test is performed to look at the mechanical quality of the solderings and avoid dry solders that could cause a subsequent failure during product life.
Functional tests: test benches (including electronic test equipements and software sequencer) are developped to check that the hardware and software blocks work properly together. These functional tests are also used to check possible issues in the system architecture or problems of interaction between components. We rely on the functional test specification developed during the prototype phases and completed during the pre-production phase.
It is often necessary to develop a specific test product firmware in order to be able to test all the functions of the product.
Safety tests: these tests ensure that the product complies with the regulations in force depending on the countries where the product will be marketed.
This electronic testing phase is key in the product quality control process as it will allow to detect the defective products before packaging and shipping.
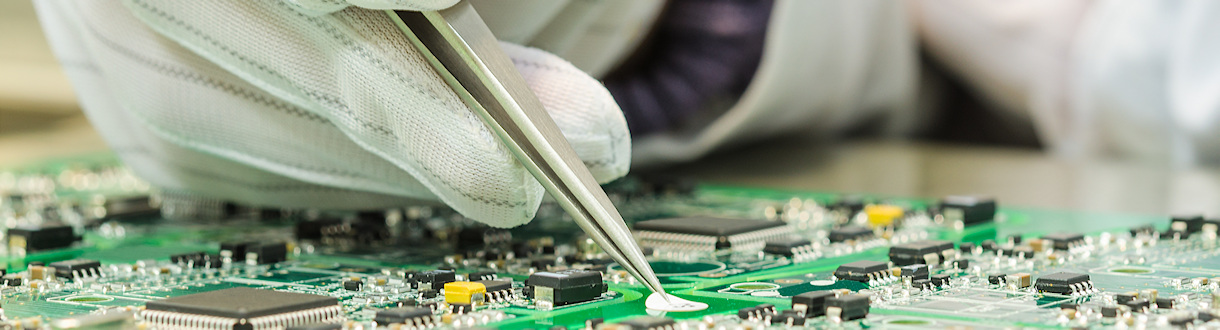
Traceability and quality test
The functional test system will store measurements made on all manufactured products. A report on each of them is issued with their individual serial number.
It is also possible to achieve product traceability by adding additional information such as product revision number, day of assembly, day of test, dates and shipping addresses, batch numbers of components, individual component identifiers, MAC radio component addresses, etc.
The test bench then generates labels with the legal traceability information: CE, RoHs, serial number, logo and address of the manufacturer. Thanks to this traceability system, we can determine the assembly and test dates of the products, as well as identify a potential defect in a manufacturing batch.
This information will be very useful for the customer’s after-sales service.
Got a project ?
TXCube brings the experience on the best way to meet your challenges. So, don’t wait and